“Infrastructure projects means local schools and local communities; it’s not just about the mega-projects in Sydney. Infrastructure is about upgrades to hospitals, upgrades to school halls, sporting facilities.”
Gladys Berejiklian, who is set to be voted by the Liberal Party room as the state’s new premier today (Monday), speaking to The Saturday Telegraph, 20 Jan.
I can’t help taking a two way bet on this. On the one hand, it is definitely refreshing to see State Governments move off the mega projects. But as school halls were a focus of the last big infrastructure spend during the economic stimulus (Building the Education Revolution), it is strange that it should still top the list of local infrastructure needs. Has this list been seriously thought through or quickly cobbled together?
Your view – populism or good decision-making?
In the last post I referred to the Economist’s idea for infrastructure decisions to be made by a ‘group for building stuff’ as if the real issue were ‘how to build’ rather than what to build – and, even more critically, why to build it – and why now? It is said that during the depression, people constructed holes and others filled them in again, as a means of keeping people employed and with an income. Now, no one wanted the holes – or they wouldn’t have been filled in again. But is it any different today, with a desire to ‘build stuff’. Perhaps we are fooling ourselves that today’s constructions are more community-valuable than those holes? If so, should we not focus on the value to be achieved, rather than the building of stuff?
The right wing think-tanks make great play with ‘mistakes’ made by governments, not excluding corruption, but ignore the fact that a large proportion of private companies fail, creating havoc for their shareholders and communities when they do. Statements such as ‘8 out of 10 entrepreneurs who start businesses fail within the first 18 months’ and ’50% of businesses fail within five years of inception’ are easy to find on the net (even if rather contradictory). Then there are the spectacular failures of older and large companies either through fraud or incompetence. Recently, there has been a flurry of suggestions that our infrastructure decisions should be made by some ‘group for building stuff’ (The Economist) or Paul Keating’s suggestion of a Reserve Bank for Infrastructure). What is the rationale for thinking that either would be superior? Comments?
“I love ‘Talking Infrastructure’ – you ask questions that I have no answers to”. (recent email from an experienced asset management trainer)
Questions for which there are answers are ideal for training courses, manuals, and instructions. Asset management, where the task is to how to choose those asset activities that best achieve the organisation’s objectives, is now, after thirty years of development, at this stage. Not everyone may know the answers but an increasing number are learning the ‘how to’ from those who do. The procedures themselves may change, a little: they may be clarified, refined, improved, but they no longer need be ‘discovered’ for that has already been done. The reason I can say this with a certain amount of confidence is that the task of ‘achieving objectives’ is a technical issue, one of optimisation under constraints.
Choosing those objectives, however, is a different matter. Clearly communicating the chosen objectives is yet another! Here we are dealing with values, and with complexity. We are in the realm of ‘wicked problems’. According to Wikipedia. “A wicked problem is a problem that is difficult or impossible to solve because of incomplete, contradictory, and changing requirements that are often difficult to recognize. The use of the term “wicked” here has come to denote resistance to resolution, rather than evil”. Incomplete, contradictory and changing requirements, well describes the problem facing those who need to set infrastructure objectives today. And, yes, they are also difficult to recognise.
How could it be otherwise where, for infrastructure decisions, the need is to plan ten, twenty, or more years into an unknowable future; where we need to juggle the needs of present v future generations, of present v. future technology, of present v. future needs, demands, values and expectations. What do we favour – economic, social or environmental outcomes? With due respect to the ‘triple bottom line’ which implies that all can be accommodated, the truth is that all conflict.
We can act as if this complexity does not exist and ‘muddle through’, a long established British tradition.
But perhaps the complexity is ‘difficult to recognise’ because we are not examining it?
‘Talking Infrastructure’ is designed to explore these difficult, complex, issues, so that we become more aware, more able to see a path through the complexity, and to debate them so that we are more able to explain whatever path we have chosen to others.
Your view?
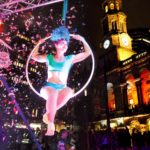
Adelaide Fringe Parade Credit: Tony Virgo
Much infrastructure serves temporary needs and is under-utilised, sports stadia for example and many arts facilities. But when we explicitly recognise that so many of our needs are time bounded, we can do better. Here are two examples.
In six weeks Adelaide will host its 56th Festival Fringe. Scheduled already are 1305 shows. This far exceeds the number of performing arts venues available, so other spaces are pressed into service including: several distilleries, the Adelaide airport, open air spaces such as the Botanic Gardens or the River Torrens, schools and colleges, sporting club rooms, hotels and cafes, shopping centres, churches and libraries, to name just some.
A festival is an explicit recognition of temporariness – and effective! During the Festival thousands of people will go to events who wouldn’t normally set foot in a gallery or a theatre. The ad hoc nature of the venue is often part of the attraction.
A temporary need doesn’t necessarily mean ‘once off’. I saw a laneway in Manila that, in the early morning, was filled with tables and chairs and provided breakfasts to workers. By 8 am, the tables and chairs had disappeared and the cooking equipment was packed away. The laneway became a packed car park. After 8 pm when all the cars and their owners had gone home, the tables and chairs came out again, this time with candles, and people gathered for conversation over a glass of something. Each of these three services were temporary, albeit continuing, and they shared the lane infrastructure.
Wanted: other examples of avoiding the need to build more infrastructure by recognising the temporary nature of needs? (Or the converse!)
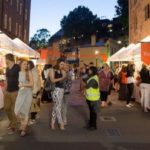
Christmas pop up market at The Rocks
Pop-ups, those temporary, transitory events and structures have lately become very trendy. Marketers love them because, as humans, we are hard wired to respond to novelty. There is also a fear of missing out if we do not take immediate advantage of what is on offer because we know there is a good chance that next time we pass by, whatever it is won’t be there. OK. If the chief characteristic of pop-ups is their transitory nature – and the chief characteristic of infrastructure is its longevity, what are we to make of a headline reading ‘Pop up Prison’?
When I saw it, my first reaction was to smile. I thought of a young and earnest journalist wanting to be up with the latest, and a harassed sub-editor, too busy to correct. After all, pop-up infrastructure is a contradiction in terms, an oxymoron. But behind the trendy term lies a more serious issue.
In New Zealand, the reference was to ‘rapid build’ which is more accurate. The cell design is one that is in use in war zones and resembles detention centres surrounded by razor wire. The cells can be rapidly deployed. This is the attraction now for cities with overcrowded prisons. In war zones rapid deployment is a response to a sudden and urgent need. It is very costly but in wartime there is not the luxury of time to plan so we wear the costs. But the same argument can hardly apply to prisons. This has grown up over many years and we have been aware of it. We just haven’t been prepared to do anything about it. Now under the cover of urgency, do we throw caution to the wind, fail to plan properly, and exacerbate our future cost problems?
It is generally recognised that around 75% of the life cycle costs of infrastructure is committed at the planning stage, when we decide where and what to build. Total life cycle costs may also be considered inversely proportional to time spent in quality planning.
Question: Why do we – both as individuals and organisations – so frequently put off thinking about, and planning for, known future contingencies until our scope for action is drastically reduced? And what can we do about it?
Infrastructure managers have long been perplexed at why more resources are not devoted to maintaining the infrastructure we put so much effort into obtaining.
Perhaps the answer lies in the fact that we really don’t want infrastructure at all, it is merely a convenient means of securing what we do want. So politicians may want the ribbon cutting and voters may want the promised jobs. Council CEOs may want the adulation (and subsequent job security and salary increases) that come from winning capital grants. What no-one particularly wants is the financial responsibility for maintaining that capital over the longer term.
Commuters don’t want a road. Few of us would get much pleasure out of simply admiring a strip of bitumen. What we do want is to get from A to B. Similarly we don’t want a power plant, or transmission wires, we do want to power up our lights and electrical appliances. Morover we don’t want prisons or law courts, what we do want is to feel safe and to be reassured that justice is served.
We may call infrastructure an asset but, once acquired, we think of it as a liability. While the announcement of a new infrastructure project is usually received with joy and jubilation, once the project is completed and the construction jobs have vanished, the mood changes. Governments, agencies and voters now unite in resenting contributing to ongoing operations and maintenance. Bi polar!
What’s the treatment? Bi polar disorder is treated with mood stabilizing drugs. The drugs change perceptions. Highs are dampened, lows are uplifted. Perhaps the answer for infrastructure is the same? Stop the nonsense of venerating new infrastructure projects as a panacea for all human ills. And equally stop the nonsense of assuming that services can continue to be provided without operations and maintenance resources. Dangerous illusions, both.
Both can be addressed by a better understanding of what infrastructure can and can’t do and a far better understanding of alternatives – this is one of our aims here at ‘Talking Infrastructure’.
And so our question today is: If you were an Infrastructure Medic – what would you do to dampen the highs and elevate the lows?
A heated holiday case study
Few today would disagree that decisions should be evidence based. But how can this be when decisions on infrastructure are decisions about the future – about future demand and future supply. Consider the following decision about the wisdom of expanding waste incineration capacity in the UK. The facts were not in dispute, but the disagreement was heated.
The facts were these. In Europe incineration had been widely adopted by member states with eight large incinerators burning more than one third of municipal waste. However, re-use and recycling are more profitable as well as sounder environmentally, so countries were doing their best to first, reduce the total amount of waste generated, and then to re-use and re-cycle as much of the rest as possible. The more successful they were in this environmental move, the less the feedstock that became available for the incinerators. Concern then started to grow over excess capacity in the expensive incinerators.
Compounding this problem was the European Commission’s green paper on “A European Strategy on Plastics” that reported that just over 20% of plastics used in Europe were recycled, half going to landfill and the rest going to energy recovery, i.e incineration. The Commission called for 100% collection rate for plastics alongside efforts by manufacturers to use plastics more sustainably and to make re-use and re-cycling easier.
Now this is where the story gets interesting. At the time, the UK had about 18m metric tons per year of incineration capacity (either existing or under construction) and about 27m tons of residual waste – or a gap of about 9m tons, material for landfill. If the EU targets were met, increasing recycling from less than 42% to over 78% it would take out all 9m tons, This was before considering reductions in commercial and industrial waste which were also subject to waste reduction programs.
Development consents had already been given for between 2m to 4m tons of further incinerator development and were continuing to be given.
Over – or under Capacity? This gave rise to a very public, and very fiery, debate between two major environmental consultants. One argued that the UK was headed for over-capacity in incineration, the other said not. Both had access to the same information given above and did not dispute it. So why were they in such disagreement?
1. They were in dispute not over the current situation but the likely future. One argued that heavy oversupply of incineration capacity in Europe would attract feedstock from the UK at more favourable prices than could be offered by local incineration. The other argued that, although there was excess supply in Europe, the export markets were volatile, unpredictable and prices unreliable and this would encourage UK facilities to regain self sufficiency and treat waste at home.
2. They also disagreed on future trends in waste generation (essentially how successful the waste reduction programs would be and how quickly they would achieve their targets).
3. But the most important source of disagreement – and one that can affect any market – was how effective the market will be in sorting out any potential oversupply. Both consultants agreed that market oversupply would have a dampening effect on new development – investors in the early stages of their development would choose not to go ahead when they saw that the market was already full. The difficulty here is how efficient and effective is the market? A perfect market would handle this with ease, but we do not have perfect markets. The consultant arguing for overcapacity said “There is a juggernaut effect as projects reach financial close which means that there will not be an immediate response to reaching capacity. Yes, new project development will eventually tail off- but there will still be a capacity overshoot due to the time lag between changing market conditions and the response to this.”
This dilemma is really about when it becomes obvious to the players that the market is already full. When can they ‘see’ it? Those who can remember when fried chicken shops were first introduced in Australia will recognise this juggernaut effect – for a period we were swamped with fried chicken shops. Over half of them were subsequently closed. However, it wasn’t until this oversupply was visible that new construction tapered off. Perhaps not so important with chicken shops, but with large and expensive public infrastructure it is a different matter.)
What are the important lessons from this story?
Analysing demand side data, unlike supply side asset data, is a matter of opinion rather than fact, because we are not looking at what is, but what might be. This is not so much a matter of evidence, but a matter of inference. It requires trend analysis and understanding markets.
In July, I went to Bali on holiday. I took my laptop, my iPhone and my iPad, admittedly, a trifle excessive, especially for a holiday. The airline then lost my luggage containing the charger cables for these devices and I was effectively ‘offline’ – for 3 days. Did I just kick back and enjoy the beautiful surroundings, the water, the massages and the respite from my inbox? After all, I was on holiday. Or did I fret?
Does the thought of being ‘unconnected’ fill you with dread? I thought of this experience whilst catching up with an article in the Guardian (from August 11, 2015) by one of my favourite authors, Brett Frischmann (“Infrastructure: the social value of shared resources”) He was suggesting that with the ‘internet of things’ it may soon become physically impossible for us to go ‘offline’. For many of us, I reflected, it may already be emotionally impossible. I was intrigued by the term ‘digital gerrymandering’ to reflect the way that Facebook, Google and others ‘influence’ us. But I was especially taken with the following proposition by Frischmann and his co-author, Evan Selinger:
“The internet of things is envisioned to be a “programmable world” where the scale, scope, and power of these tools is amplified as we become increasingly predictable: more data about us, more data about our neighbours, and thus more ways to shape our collective beliefs, preferences, attitudes and outlooks. Alan Turing wondered if machines could be human-like, and recently that topic’s been getting a lot of attention. But perhaps a more important question is a reverse Turing test: can humans become machine-like and pervasively programmable.”
Brett speaks to this idea in a short interview on YouTube
The question that this raises for me is: in this programmable world, how valid are our ‘community consultations’? Is there any role left for us, as citizens, as community, to impact infrastructure decisions?
A time for gratitude. The Talking Infrastructure Blog started on July 29 and since then, with the help of Mark Neaseby, Gregory Punshon, Jeff Roorda and Geoff Webb (thanks guys!) we have uploaded 46 posts and attracted 80 comments.
Our thanks to all readers for their presence here and I hope that it has got you thinking more about infrastructure decision making. And for those special readers who submit comments, let me say that I regard each and every one of them as a present and I take great delight in unwrapping them and discovering the truths they reveal. It is a curiosity of the complex world of infrastructure decision making that we can all much appreciate the arguments of others even whilst arguing against!
And if you should choose to use the holiday break for some practical or philosophical reflection on IDM issues -know that the web is always open!
Recent Comments